富士吉田工場がFSSC22000認証を取得!!
CLYTIA、PREMIUM WATERの山梨富士吉田工場では、食品安全マネジメントシステムの国際規格であるFSSC22000の認証を取得いたしました!
山梨富士吉田工場は国際基準FSSC22000認証を取得しました
FSSC22000は、食品安全マネジメントシステムの1つで、オランダのFSSC(The Foundation of Food Safety Certification:食品安全認証団体)が、食品安全マネジメントシステムの国際規格であるISO 22000と、それを発展させたISO/TS 22002-1(またはISO/TS 22002-4)を組み合わせて開発した規格です。
国際食品安全イニシアチブ(GFSI)が制定したベンチマーク承認規格です。
生産開発本部品質保証部 小俣さんに聞きました。
–ISO9001とFSSC22000の違いを教えてください
「ISO9001」は品質マネジメントシステム(Quality Management System)で、お客様に良い製品をお届けするプロセスを管理するシステムを管理するのが目的です。
そのプロセスは社内で規定することができるため、必ずしもすべての要求事項を適用しなくてもよいのです。
「FSSC22000」は、「ISO22000食品安全マネジメントシステム」より更に、すべき項目をより具体化し、かつ、規定の前提プログラム(PAS220シリーズ)を定め、なおかつISO22000でカバーしきれなかったフード・テロ、原材料やアレルギー物質の管理などや、食品安全に関連する要員の監視などの「追加要求事項」を含む、すべての要求事項に関して適用されていなければ取得することができませんので、取得は比較にならないくらい難しいものです。
–なぜFSSC22000認証を取得することになったのですか?
山梨富士吉田工場では、以前より「ISO9001」を取得し、お客様に製品をお送りするまでのプロセス管理を実施しておりましたが、よりお客様に安心してお水をお届けできるよう「FSSC22000」認証取得を目指しました。
取得は難しかったですが、大手企業も取得を勧めている「国際基準」の規格なので、お客様に安心安全なお水を自信をもって提供できます!
–具体的にどういうものですか?
例えばペットボトルですが、購入している場合は、その購入業者の衛生状況、また、ペットボトルを運ぶトラックやコンテナの衛生状況まで管理する必要があります。
次にハザード(危害要因)分析です。
生物的、科学的、物理的な危害要因をすべて洗い出し、許容限界を超えないように管理する仕組みを作ります。
例えば「井戸」に対してのハザード分析なら、
・ポンプの故障
・地下水の汚染
・人的な細菌汚染
などなど、考えられるものをすべてピックアップします。
–何が一番大変でしたか?
コンサルタントを導入して取得するのが一般的なのですが、今回はみんなの力で取得しよう!!とすべて自分たちで行いました。
そのため、一次審査の際に審査員の方々にコテンパンに言われてしまって。。。
その後、若手が主体になり、一からすべてのラインを調べなおし、機械についても取扱説明書を穴があくまで読み、井戸からお客様にお水をお届けするまでのすべての工程をひとつずつピックアップしました。
今までも、工場などビデオカメラの設置がありましたが、書類の管理も要求事項のひとつなので、書類の出し入れまで確認できるようにするため執務スペースにもビデオカメラを取り付けました。
「FSSC22000」の要求事項は、「なにかあったら」、ではなく、なにか「ない」ように、「ない」ことに対して想定し、「ない」ことを前提にしている活動。
その代り、「それ」が徹底できていれば事故は必ず起きない。
ただ、それを現場の方々に理解浸透させることも重要です。
–導入して気づいたことは?
今まで「当然」として行ってきていたことを改めて見直すいい機会になりました。
例えば、ボイラーで使用している溶剤なども、証明書を取得し、使用したことを記録に残し、正しく管理できている状態にしているし、作業着についてもボタンやポケットがないものに変更しました。
–FSSC22000認証を取得し、今後の展望は?
FSSC22000認証を取得できましたが、取得することが目的ではなく、取得後、いかに「継続」するかが大事だと思っています。
1年更新なのですが、隔週でこれらの要求事項がすべて実施できているかを各部署、資料を持ち合い確認しています。
そのために担当者は、「内部監査委員」の資格を取得しました。
また、定期的に内部監査委員が、要求事項に対し、現場の確認をしたりヒアリングをし、帳票類も確認しています。
例えば給湯室にある洗剤ひとつでもリスト化されていないものがあれば観察事項としてチェックします。
また、新しい材料、手順、機械などが導入されれば、それを追加していくことも必要です。
次の審査まで『Plan(計画)→ Do(実行)→ Check(評価)→ Act(改善)』を繰り返します。
手前味噌ではございますが、工場見学をするたびに、少しずつレベルアップしていて、お客様に自信をもってお届けできる商品だと自負しています!
これからも富士吉田工場は、お客様に安心安全なお水を安定的にお届けできるよう全員一丸となって頑張りますので、引き続きご愛飲よろしくお願いいたします!
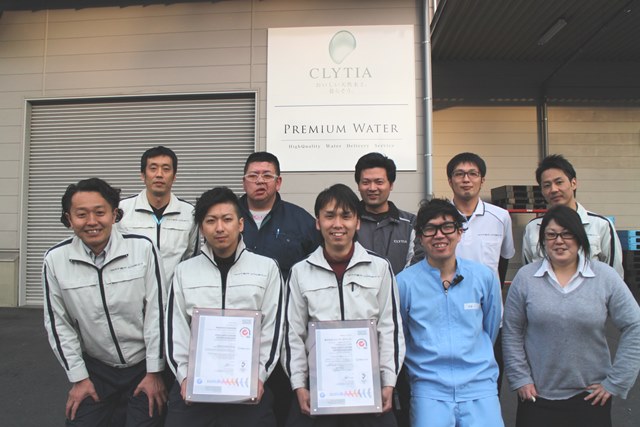